PSC Automation
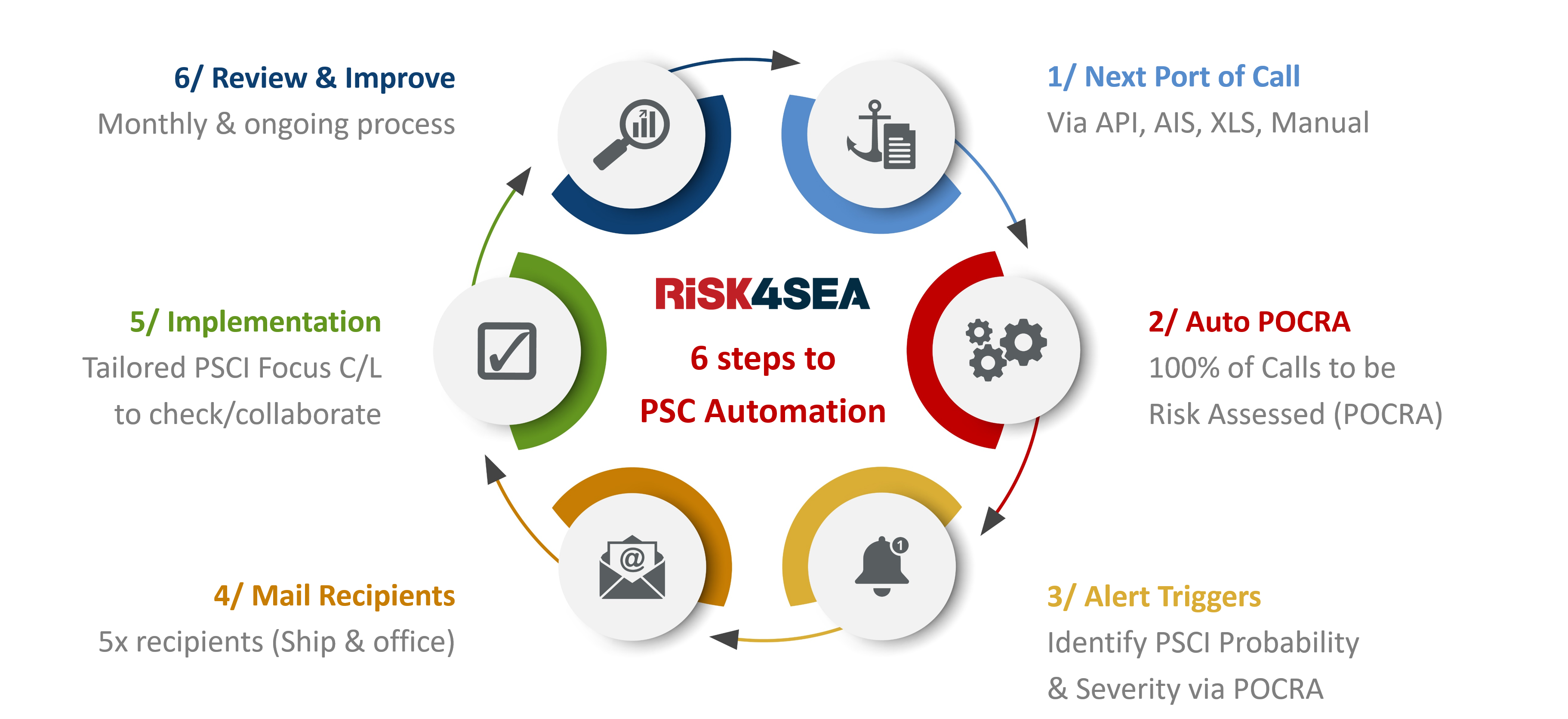
Objectives of a PSC Strategy
To achieve PSC Excellence, a well-defined strategy should focus on three key objectives, listed by priority:
- Eliminate Detentions – This is the only non-negotiable goal.
- Minimize Deficiencies – Reducing deficiencies enhances compliance.
- Minimize Noise – Filtering out unnecessary data improves decision-making.
Since minimizing deficiencies and noise often involves trade-offs, it is crucial to carefully evaluate how and when these settings should be applied.
Why PSC Automation Matters
Our analysis, outlined in the POCRA PSC Risk Levels Matrix, highlights key insights into risk management. Contrary to popular belief, detentions can occur at any risk level. In fact, only 60% of detentions happen at ports where PSC inspections are expected (i.e., during an open PSCI window), and the port is deemed most challenging.
The most critical risk level is PRL 6, where 7% of inspections at closed-window ports lead to 17% of detentions. This underlines the importance of assessing 100% of port calls for risk—automatically—initiating efficient processes that save time while increasing reliability by over 950%.
How We Do It
We implement PSC Automation through six (6) key steps:
Step 1: Identify Next Port of Call
We track the next port call through various methods—via AIS, API integration with clients, XLS upload of scheduled calls, or manual input by users.
Step 2: Automated POCRA
With ship and port data, we automatically conduct a Port Call Risk Assessment (POCRA) for 100% of calls, including multiport assessments for consecutive calls.
Step 3: Alert Triggers
The POCRA results determine the PSC Risk Level, triggering automated actions like email alerts, checklist requests (via web or mobile), and more, tailored to user preferences. Advanced settings allow customization for ships, fleets, ports, and countries.
Step 4: Alert Recipients
Alerts can be sent to multiple recipients, including ships and shore locations. Emails are fully customizable, incorporating ship-specific details in the subject, body, attachments, and recipients.
Step 5: Implementation
The core of implementation involves completing a tailored checklist, specific to the ship, manager, and port. Each checklist is fully prioritized, with designations for:
- DET – Detainable Items
- CIC – Concentrated Inspection Campaign Deficiency Codes
- CSP – Common Deficiency Codes between Ship and Port
- CMP – Common Deficiency Codes between Manager and Port
- S10 – Top 10 Ship-Specific Deficiency Codes
- C10 – Top 10 Company-Specific Deficiency Codes
Step 6: Review & Continuous Improvement
The review process occurs on a monthly, quarterly, and annual basis, covering:
- What worked and what didn’t
- Hit/miss assessments
- Feedback from ships and office teams
- Integration of unannounced local PSC FIC
- Fine-tuning and further refinement of the overall process
Experience it Firsthand
Should you be interested to have an actual taste of the experience please contact our team for a FREE Trial
Dive Deeper
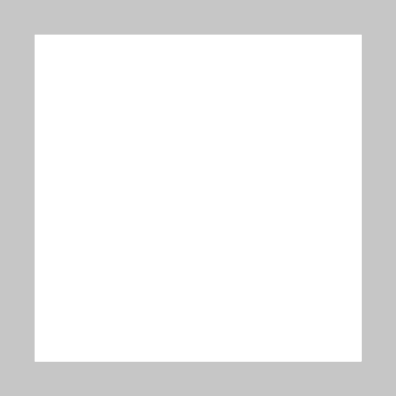
PSC Intelligence
Powered by PSC Inspections
We host the largest and most comprehensive PSC intelligence database, going beyond just PSCIs and deficiencies. Our platform offers deep insights into actual inspections, from calculating PSCI windows for every port call to generating tailored checklists for specific ports, ships, and managers—ensuring everything is prepared efficiently and effectively.
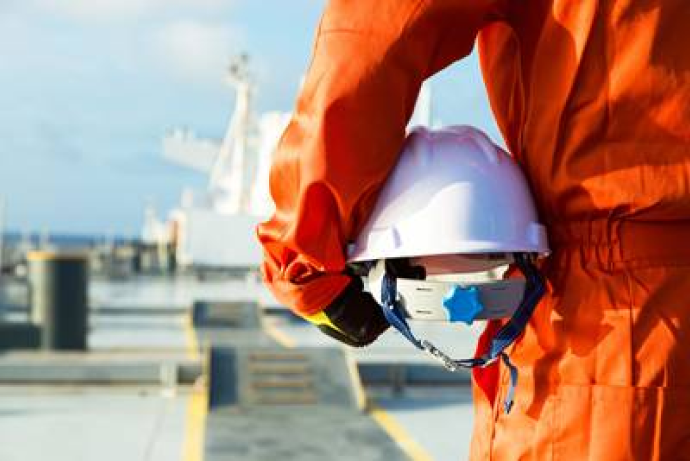
PSC KPIs
Explore DPI, DER & KPIs vs Ship Age on specific Ports
Challenging Ports
Take a deep dive into the most challenging ports
POCRA
Get POCRA for your Ship @ next port of Call with Real Data
Best Performers
Find the top performers on each fleet segment
PSC WiKi
Explore & learn from the latest PSC Procedures